Enhancing Biological Nutrient Removal: Nansemond WWTP
When the Hampton Roads Sanitation District (Suffolk, VA) needed to increase the capacity of its Nansemond WWTP to accommodate its growing service area and faced stricter nutrient level discharge standards, HRSD retained Hazen and Sawyer to evaluate alternatives for expansion and achieving BNR goals.
Project Outcomes and Benefits
- Designed a plant expansion and upgrade that meets a total nitrogen limit of 8 mg/L year-round and 1 mg/L total phosphorus year-round. This includes new supplemental carbon feed facilities capable of utilizing methanol, ethanol, glycerin, MicroC, corn syrup, or acetic acid.
- Upgraded to provide sidestream treatment of centrate using the Ostara process and a backup ferric chloride addition system using an abandoned pretreatment structure to precipitate phosphorus and equalize the return stream.
- The plant upgrade included improvements to hydraulic distribution channels, to further enhance process performance and ease of operation.
- Upgraded the aeration system to include three separate dissolved oxygen control zones to optimize BNR and optimize supplemental carbon addition.

Paul Pitt is a leading expert in wastewater treatment plant design and operation and serves as Hazen’s Director of Wastewater Technology.
Related Topics:
Expanded Capacity, Upgraded Capabilities
The plant expansion and upgrade meets a total nitrogen limit of 8 mg/L year-round and 1 mg/L total phosphorus year-round.
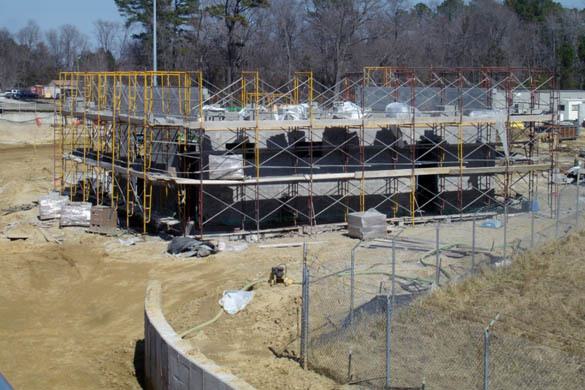
Hazen and Sawyer has been involved with all of the major design and construction at the Nansemond Treatment Plant and recently designed biological nutrient removal (BNR) facilities such that the existing 30-mgd plant will meet an annual average total nitrogen of 8 mg/L. On previous projects, Hazen and Sawyer provided process evaluation, design, construction management and start-up services, O&M manuals and operator training for expanding and upgrading the Nansemond plant from 10 mgd secondary to 30 mgd.
Hazen and Sawyer provided the same basic services on the design of the original 10-mgd facility construction in the 1980s. The latest design provides for an advanced 5-stage BNR treatment process. The facility is designed to meet a total nitrogen limit of 8 mg/L, year-round. Chemical precipitation of phosphorus using ferric chloride was also incorporated into this design as a backup to ensure compliance with the required effluent limits.

Sidestream treatment of centrate is also included as a part of the latest upgrade. The sidestream treatment is primarily designed to remove phosphorus. One sidestream treatment option is the Ostara process, which will participate the phosphorus out as struvite pellets – marketed as slow release fertilizer.
The plant expansion also included hydraulic distribution channeling design features to enhance process performance and ease of operation. New and existing facilities were combined into a single process flow train. Equal flow and solids distribution under all flow conditions are provided.
Other features of the design include new screening, grit, primary settling, final settling, and chlorination/dechlorination facilities. Sludge handling facilities include gravity belt thickeners, high solids centrifuges, and truck loading facilities. The preliminary engineering included wetlands delineation, environmental assessments, and securing all Federal, State and local permits.
Considerable process flexibility was incorporated into the BNR facility design. The plant can operate in 3-stage mode in the winter to avoid unnecessary additional construction, VIP mode, 5-stage BNR + VIP mode, and 5-stage BNR mode. There is also the flexibility to change process conditions, such as internal recycle flows and vary the anaerobic, anoxic, and aerobic mass fractions.