This Machine Could Solve the Biggest Problems in Biosolids
Supercritical water oxidation destroys sludge in seconds. A team of engineers is helping a California utility become one of the first to harness it.
ONE MORNING IN MARCH, in a manufacturing plant in Kokomo, Indiana, Lynn Grijalva stood before a table displaying a beaker of sewage sludge, some pitchers of clean water, and two cans filled with minerals: one wet, one dry. She dug her fingers into the latter.
“It’s coarser than flour, but still really fine,” said Grijalva, a Vice President at Hazen. “There’s 20% phosphorus in it. You could easily use it to make fertilizer.”Nearby sat two connected 40-foot shipping containers. Sludge like what was in the beaker had been fed into them. Thanks to new technology called AirSCWO™, all that came out was the water and minerals, plus a tiny amount of carbon dioxide and nitrogen gas.
Related Topics:
The AirSCWO 6 unit on display at the plant in Kokomo, Indiana

A container of wet minerals produced by the AirSCWO system. (The minerals come out of the system mixed with water.)
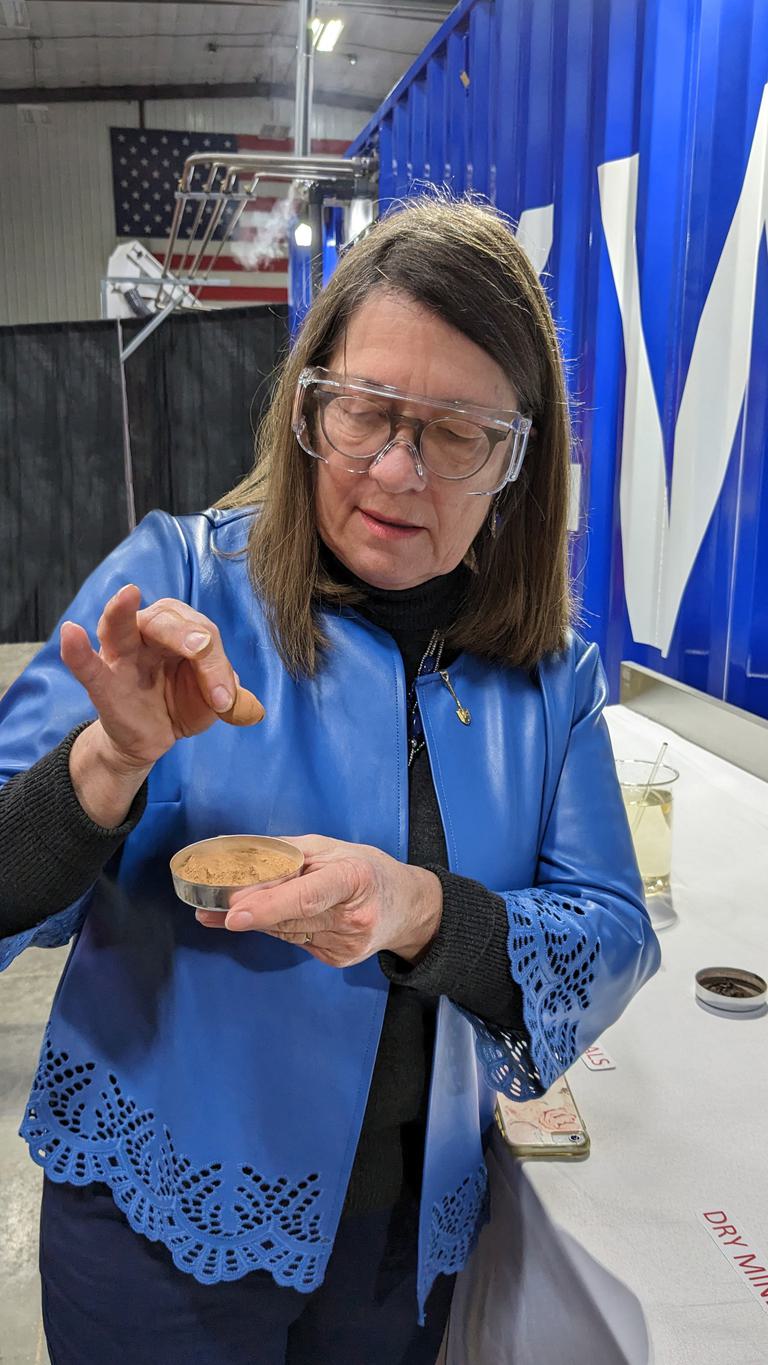
Hazen Vice President Lynn Grijalva holds up a container of fully dry minerals produced by the AirSCWO system behind her at the plant in Kokomo, Indiana.
SCWO stands for supercritical water oxidation. As kids, we learned that water exists as a solid, liquid, or gas. But extreme heat and pressure can transform it into a fourth state called supercritical water.
Add oxygen to supercritical water, and it becomes the chemical equivalent of Hercules, capable of destroying almost all organic matter—even chemicals like PFAS—in seconds. The process can also cut total solid mass by more than 95%. If you start with 100 pounds of organic solids, that means ending with five.
Mohammad Abu-Orf thinks SCWO could potentially solve multiple big challenges in the field of biosolids (treated sewage sludge), from rising disposal costs to chemical contamination.
“This could be the Holy Grail of waste management,” said Abu-Orf, a Hazen Vice President who leads the firm’s biosolids group.
The AirSCWO unit in Kokomo—engineered by 374Water and built by the Merrell Brothers, the owner of the manufacturing plant—is one of the first commercial SCWO systems. It’s called AirSCWO 6 for its ability to treat six wet tons of sludge per day.
Soon, the system will be shipped to California, where both companies and a Hazen team led by Grijalva will help the Orange County Sanitation District (OC San) become one of the first utilities to test AirSCWO at significant scale. The unit will operate for 18 months.
“If it succeeds—and we think it has a really good chance—this could be a revolutionary technology for biosolids management,"
Abu-Orf said.

“I need alternatives”
OC SAN SERVES 2.6 MILLION PEOPLE in an area just south of Los Angeles. With the Orange County Water District, the utility recently finished expanding an innovative system that turns wastewater into drinking water, then injects it underground to replenish groundwater.
But wastewater isn’t OC San’s only responsibility. The agency’s two wastewater treatment plants generate 800 tons of wet solids daily. The sludge goes through huge digesters that consume organic material and generate methane gas. What’s left over is dried in centrifuges and trucked away, much of it to farms as fertilizer. Rob Thompson, OC San’s general manager, said the utility spends $12 million per year just transporting biosolids to farms and composters.
“And California is saying no more diesel trucks,” he said. “Well, we’re shipping our stuff from Orange County to Yuma. That’s about an 8-hour round-trip haul. An electric truck won’t make that. So that’s going to get much more expensive.”
Meanwhile, PFAS—chemicals used in countless consumer products and linked to various health risks, including some cancers—have been detected in sewage sludge around the country. Current biosolids technologies don’t destroy these notoriously resilient chemicals. For that reason, Maine recently banned the application of biosolids to crops. Wastewater plants there have scrambled to find other destinations for solids.
Other contaminants found in sludge, like pharmaceuticals and microplastics, could throw more curveballs in the future.
“It seems like long-term, it’s just a matter of time until we aren’t allowed to reuse biosolids or burn methane anymore,” Thompson said. “I need alternatives.”

Marc Deshusses stands in the AirSCWO prototype he developed at Duke University, where he teaches civil and environmental engineering. The dark vial in his hand holds contaminant-laden water from a landfill: one of many kinds of organic waste AirSCWO can convert into clean water (as shown in the jar), minerals, and trace gases.

The 374Water team named the AirSCWO 6 unit (above) “Ana,” after anadromous fish, which spend much of their lives in oceans before swimming up rivers and streams to spawn. “We think the upward movement, from saltwater to freshwater, is inspirational,” Deshusses said.
“A pressure cooker on steroids”
MOHAMMAD ABU-ORF SPENDS MANY of his working hours looking for such alternatives.
“Part of my job is to keep an eye on innovative technologies for biosolids management and treatment,” Abu-Orf said. “A few years ago, I heard of this company, 374Water, developing this prototype for a SCWO system.”
Marc Deshusses first created the system as part of a Gates Foundation project to develop innovative toilets for developing countries. SCWO had been around since the ‘80s, but other attempts to harness it had largely failed. Deshusses, a professor of civil and environmental engineering at Duke University, used that prior research to hone his design.
The result was “a pressure cooker on steroids,” Deshusses said. His system combines sludge and air in a reactor, where extreme heat and pressure—at least 374 degrees Celsius (705 degrees Fahrenheit) and 3,205 pounds per square inch (218 atmospheric pressure)—instantly turn the water supercritical. The process breaks down organic matter in seconds, while the resulting heat is recycled to power the next reaction.
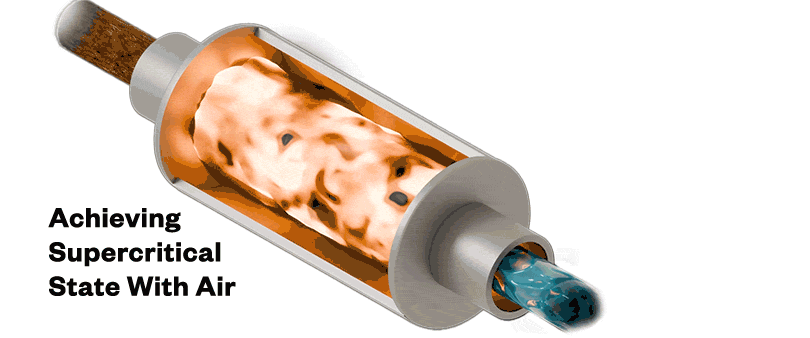
Every organic material Deshusses and his researchers fed into the prototype—food waste, chemical waste, landfill leachate—was destroyed.
“One day we decided to put some PFAS in there and see what happened,” Deshusses said. “We put a lot in, but we didn’t find any in the output. Zero.”
Since then, multiple experiments have proven that SCWO can eliminate more than 99% of identifiable PFAS, leading the U.S. Environmental Protection Agency to call it a “promising” PFAS destruction technology.
Deshusses eventually patented his SCWO system and co-founded 374Water with fellow Duke engineer Kobe Nagar to commercialize it. When Abu-Orf visited Duke in 2019 to see the device in action, he knew the startup was onto something and began helping them apply for grants and awards.
The first big road trip
THOMPSON WAS SIMILARLY ENTHUSED when he read a story about 374Water in late 2020.
“I saw what they were doing and slapped my forehead and said, ‘Wow,’” Thompson recalled. “‘These guys have a better mousetrap.’”
Within a year, OC San’s board approved an $8.7 million demonstration project, which will bring AirSCWO 6 to the agency’s Fountain Valley plant. (The federal government later committed another $3.45 million to the work.) Installation will start once the unit gets a state air permit.
In the first six months of operation, 374Water will run the unit and train plant staff until they’re ready to take over. Hazen Senior Associate Derya Dursun—who directs the firm’s biosolids research and helped with permitting for the project—will lead a performance analysis.
“We’ll be monitoring a lot of details,” said Dursun. “PFAS and microplastics are a big concern, for example, so we will look at the ability of this technology to destroy those emerging contaminants.”
But Grijalva stressed that AirSCWO is a proven commercial product. In other words, this isn’t an R&D project: It’s more like taking a new kind of car on its first big road trip.
“When you’re running the first one for the first month, the first year, what you want to know is, can it run reliably?” Grijalva said. “This is about making sure it runs with no stops and no hiccups. After that, then you fine-tune it.”

If all goes well, an AirSCWO unit that can treat 30 wet tons per day—and generate net-positive energy—will replace the original. Hazen Senior Associate Ian Mackenzie designed the plant connections to work for both sizes, and the AirSCWO 6 has sludge dewatering equipment that’s also compatible with the bigger size.
Thompson sees multiple ways the larger unit could save energy within his plants’ existing treatment systems. Eventually, he said, SCWO tech could process all of OC San’s biosolids, and maybe even help landfills with leachate and food waste, and drinking water plants with spent PFAS filters.
“I believe our industry needs to be more aggressive about saying where we want to go, and where science and engineering can take us to make the world better,” Thompson said. “This thing will probably work. Will we have metallurgical problems along the way? Maybe. Will the machines need some tweaking? Probably. Does serial number one look exactly like serial number two? I hope not. It’ll get better.”
