From Conventional Wastewater Facility to Membrane Bioreactor
Challenges of Retrofitting Your Facilities
Last Modified Jul 05, 2022

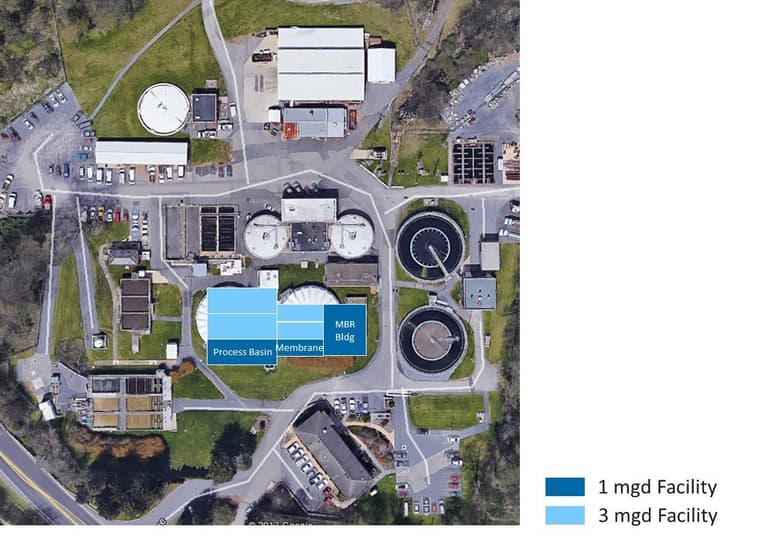
The Pennsylvania State University (PSU) owns, operates, and maintains a conventional active sludge wastewater treatment plant (WWTP) located in State College Borough and College Township, Centre County. The WWTP has been in operation since the early 1900s and provides sanitary sewer service to a majority of the University Park Campus and a small portion of the State College Borough in the College Heights District. Wastewater treatment facility upgrades are required to improve operational reliability, replace aging infrastructure, improve treatment performance and efficiency, and upgrade the process to meet Pennsylvania Department of Environmental Protection (PDEP) Class A reclaimed water standards. Penn State has constructed reclaimed water infrastructure on the University Campus with the goal of using high quality reuse water for campus needs. Penn State commissioned the Haskell and Hazen and Sawyer Team to select a treatment technology and design and construct the WWTP upgrades using a progressive design build process.
The University is faced with several challenges associated with the existing WWTP site. The WWTP is restricted to a small area between the campus, a highway, and Thompson Spring (an environmentally sensitive area). The WWTP site is also located within the Spring Creek watershed, which is designated as a high quality cold water fishery. One of the University’s goals is to limit the WWTP upgrades to be constrained within the existing constructed WWTP footprint to minimize potential impacts to the watershed and Thompson Spring. The existing WWTP must also remain in service during construction. Other challenges include regulatory compliance with Pennsylvania’s reclaimed water standards, evaluation of treatment alternatives, hydraulic constraints, the MBR procurement process, and design challenges associated with the new MBR facility.
The current Penn State WWTP has a permitted hydraulic capacity of 4.0 million gallons per day (mgd). Flows to the WWTP have been decreasing over the past 20 years, which was attributed to a number of Penn State water sustainability initiatives including proactive water conservation programs, the development of a central chilled water system that allows for the decommissioning of once through cooling systems, and the elimination of sources of inflow and infiltration into the sanitary sewer collection system. Additionally, the permanent diversion of State College Borough flows from the PSU WWTP to the University Area Joint Authority was completed in 2016. Based on future wastewater flow projections for the University Park Campus, a 3.0 mgd design capacity was recommended for the upgraded WWTP with provisions for expansion to 4 mgd.
Challenge 1: Regulatory Requirements
Effluent disposal for the PSU WWTP consists of spray irrigation to the University’s Living Filter via a Water Quality Management permit. The Living Filter is a combination of dedicated agricultural and forested acreage equipped with spray irrigation system infrastructure. Treated effluent is conveyed from the WWTP site to the Living Filter via an effluent pump station. The effluent disposal requirements for the Living Filter include biochemical oxygen demand (BOD), total suspended solids (TSS), fecal coliform, pH, monthly average total nitrogen of 23 mg/L, and residual chlorine.
In September 2017, PSU received authorization to install a new reclaimed water system infrastructure via a second Water Quality Management permit. The reclaimed water permit outlines the beneficial uses for various systems on the University campus and the corresponding class of water use, e.g., Class A+, Class A, Class B, and Class C. PSU anticipates that the proposed WWTP will be designed to treat to a Class A beneficial use. Class A reclaimed water effluent permit requirements are more stringent than the effluent disposal requirements for the Living Filter. Class A permit requirements include carbonaceous BOD (CBOD), total organic carbon (TOC), turbidity, total nitrogen, stringent fecal coliform limits, total organic halides (TOX), residual chlorine, and quarterly monitoring for all primary and secondary drinking water contaminants. The Class A effluent limit for total nitrogen is less than 10 mg/L, which will require that nitrification and a denitrification nutrient removal process be incorporated in the design of the new WWTP.
Challenge 2: Treatment Alternative Evaluation
Influent flow is conveyed through a pretreatment facility for grit removal and fine screening followed by primary clarification. Primary effluent is then split between three process trains: trickling filters (installed in the mid 1950’s), an anoxic tank (installed circa 2000), and an activated sludge treatment train (installed in early 1960s). Trickling filter effluent and anoxic basin mixed liquor combine in aerated treatment tanks, which are followed by the final settling tanks. Originally, the WWTP infrastructure included four final settling tanks, two of which were formally retrofitted from final settling tanks to the aeration treatment tanks in the late 1990s. The activated sludge process (ASP) treatment train includes final settling integral to the process. All clarified effluent is disinfected via chlorination prior to pumping to the Living Filter for final effluent disposal.
During the conceptual design phase, it was recommended that the majority of the existing treatment infrastructure be replaced. Based on evaluations by PSU staff and their consultants, numerous deficiencies were identified at the existing PSU WWTP. Most of these deficiencies were associated with aging infrastructure that has exceeded or is nearing the end of its useful life. Additionally, older equipment and technologies used at the PSU WWTP were anticipated to create challenges to improving the quality of the effluent to meet PDEP reclaimed water standards.
The existing PSU WWTP is located adjacent to an environmentally sensitive area, Thompson Spring. The WWTP site is also located within the Spring Creek watershed, designated as a high quality cold water fishery. One of PSU’s goals was to limit the upgrades of the WWTP to be confined within the current WWTP site footprint to minimize additional development of the site and minimize potential impacts to Thompson Spring and the watershed. Therefore, high biomass inventory alternatives were selected for the detailed evaluation in comparison to conventional activated sludge treatment. The high biomass inventory alternatives were anticipated to be able to provide a greater level of treatment in smaller tank volume and minimize the footprint impact to the WWTP site.
Four high biomass inventory alternatives were developed and evaluated to upgrade the PSU WWTP. The four alternatives included conventional activated sludge, membrane bioreactor (MBR), BioMag®, and integrated fixed film activated sludge (IFAS). A detailed evaluation of the four alternatives was conducted giving consideration to cost, facility requirements, operational and maintenance requirements, and regulatory requirements. Each evaluation criteria is associated with multiple parameters. Operation and maintenance parameters included treatment reliability and redundancy to consistently achieve permit limits, system flexibility, operability, energy efficiency, technology experience, and market competition.
The technical evaluation revealed that the trickling filters were only used a few hours a day for peak flow management. Biological process simulations, supported by detailed sampling events, and PSU staff operation of the anoxic and ASP trains supported the decommissioning of the trickling filters to reclaim site footprint for construction of the new facilities while maintaining the WWTP in operation and regulatory compliance. Of the four technologies evaluated, the MBR and BioMag® technologies provided the more optimal site footprints.
The evaluation included a detailed analysis of each of the four treatment technologies and respective technology advantages and disadvantages. The technology options could not receive the same rank for the same parameter, as the purpose of the ranking was a comparison of the four technology options relative to one another. The lowest overall total score indicated the highest ranked technology option.
Submerged MBR technology resulted in the lowest score and therefore the highest ranked technology option. MBR technology provides a flexible process in a compact footprint and a high quality effluent suitable for a wide range of applications. MBR technology is more energy intensive than conventional activated sludge. Conventional activated sludge ranked as the second highest technology option. Conventional activated sludge is similar to MBR technology in process flexibility and operability. However, conventional activated sludge has a larger campus style footprint compared to MBR technology. BioMag® and IFAS ranked third and fourth, respectively. The BioMag® technology yields an effluent quality suitable to many applications; however, this technology is fairly new to the industry with limited installations. Both BioMag® and IFAS technology options are energy intensive and require a campus-style footprint similar to conventional activated sludge. IFAS technology offers increased capacity in a smaller footprint compared to conventional activated sludge; however, the maintenance issues and material handling of the IFAS media ultimately resulted in the lowest rank of the four technology options.

Challenge 3: Hydraulic Constraints
One of the earliest recognized challenges in the conceptual design phase maintaining the existing WWTP in service during construction. The recommendation that the trickling filters be removed from service to reclaim site footprint for construction of new infrastructure required that flow needed to be distributed properly between the anoxic treatment and ASP trains. A hydraulic model was developed to evaluate the hydraulic baseline conditions with respect to the number of units in service, address the challenges of limited flow control, and evaluate hydraulic capacity of existing infrastructure.
Challenge 4: MBR Procurement Process
PSU solicited bids for the procurement of the MBR treatment system at 30 percent design via a Technology Request for Proposals (RFP). The membrane system scope of supply specified in the RFP included the membranes, membrane housing, and associated support structures; permeate pumps and appurtenances; permeate air headers; entrained air separation system; air scour blowers; chemical feed systems; membrane integrity system; compressed air system; motors; control panels; and all valves and instrumentation necessary for a complete membrane system operation. The bidders were required to provide a treatment system designed to treat an average day flow of 3 mgd and include the number of membrane units required for the future expansion to 4 mgd. Flow greater than 2Q mgd are to be diverted to influent equalization.
Technical specifications for both the hollow fiber and the flat sheet membrane types were included in the RFP. The footprint differences between the hollow fiber and flat sheet membrane types were significant. Both membrane system types were specified to be designed in an N+1 configuration, e.g., full treatment capacity with one membrane tank out of service. For the hollow fiber design, the plant expansion options included constructing an empty membrane tank for additional membrane skids or leaving spare space in operating membrane tanks such that additional skids may be for expansion. Due to the larger footprint of the flat sheet membrane system, spare space was specified to be left in the existing tankage for the expansion from 3 to 4 mgd. Treatment credit was not given to the volume associated with the MBR tanks.
The RFP included a set of evaluation criteria by which all bid proposals were ranked. The highest points that could be achieved was 100. Manufacturer experience was worth 20 points. Points were awarded for MBR experience associated with operating facilities that were achieving total nitrogen less than 10 mg/L and ammonia less than 1 mg/L. The technical approach was assigned a 30 point maximum. Technical points were evaluated on the basis of the MBR supplier meeting the requirements of the technical specifications and basis of design. The Membrane Manufacturer Services criteria was assigned 16 points and included membrane supplier representation and assistance, local technical support, 24-hour technical services, and if an annual service contract was available by the membrane supplier. Financial responsibility was worth four points. The cost proposal was assigned 30 points. Capital costs include the cost of the equipment provided in the scope of supply and the structural cost of the membrane tankage and appurtenances (e.g., size of bridge crane required, etc.) specific to the membrane supplier. Life cycle costs included operational costs associated with energy and chemical consumption for maintenance and recovery cleaning.
Based on the detailed evaluation of the proposals, Hazen recommended to Haskell and PSU that contract negotiations be conducted with Evoqua, the highest scoring MBR Supplier. Evoqua was ultimately awarded the contract to supply the membrane system for the PSU WWTP expansion and upgrade.
Challenge 5: Design Challenges
There were several design challenges associated with the PSU WWTP expansion project. The PSU WWTP expansion is large and impacts a large number of university departments and stakeholders. Several of the most significant challenges are summarized as follows:
- MOPO considerations and construction of new infrastructure within the existing WWTP footprint.
- Minimizing impacts to environmentally sensitive areas.
- The elevation change on the site was significant, which required consideration for access to equipment for maintenance and operation.
- Matching new WWTP buildings with the existing university architectural style.
- Documenting ahead of design all the existing electrical infrastructure associated with the existing PSU WWTP.
- Easement challenges associated with a new site access road off of a busy university thoroughfare.
- Managing stormwater on the site, as the majority of PSU’s stormwater discharges on the WWTP site.
- Temporary utility relocation prior to construction.
- Temporary relocation of other PSU Department staff currently housed on site.
- Construction sequencing and phasing.
- Process considerations for expansion.
Given the WWTP site constraints with respect to the new design, a solution was found to minimize constructed tankage in the current project against future expansion needs. To minimize project costs, new primary clarifiers were removed from the project. Three process trains are required to treat 3 mgd. For expansion to 4 mgd, additional process tankage is not required provided that the primary clarifiers are constructed. This solution minimizes the impact to the plant footprint and existing structures as well as alleviates construction concerns in the next expansion project.
Conclusions
Project implementation will continue via the progressive design-build delivery method. The project will transition into the construction phase in early 2019. Construction is anticipated to continue through late 2022 with plant start-up near the end of 2022.
The PSU WWTP expansion and upgrade project is an example of a successful partnership between the Owner, Contractor, and Engineer. Decisions were thoughtfully made in a timely manner. Also, the Owner provided significant comments and involvement in the operation and maintenance of the proposed MBR facility.